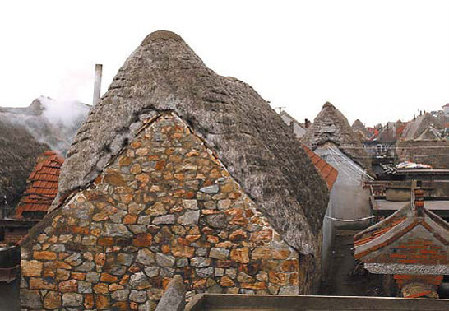
Seaweed bungalows are indigenous architecture in Rongcheng, Shandong province. Ju Chuanjiang / China Daily
It is a rainy afternoon, a perfect occasion to indulge in nostalgia and share memories with a visitor from afar. Yu Shoushui, 65, is relaxed and eager to count off all the advantages of his little heritage bungalow made from seaweed harvested from the nearby shores.
He has lived here for decades, sharing his home with his 83-year-old mother.
"Nothing, not even a modern two-story building, can persuade me to move out," he declares.
His house, he says, is cool in summer and warm in winter. The grass roof can stand up to the strongest winds, and the house is good looking. But he has to admit that his little hamlet of seaweed bungalows is now a village full of the elderly.
The old folks acknowledge that the modern new homes are indications of the better possibilities of life, but they feel that it is the unique seaweed homes that carry their cultural heritage.
The history of Rongcheng's seaweed bungalows can be traced back to the Qing Dynasty (1644-1911), and they were already common structures from the Yuan Dynasty (1271-1368).
It was said that the ancestors of the Rongcheng villagers started using eel grass as roofing material after they found that the dried grass was very pliable and tough. The tradition was passed down through many generations, each improving on the accidental discovery until it became part of the regional architecture.
Eel-grass thatched roofs are insect-proof, mold-resistant and fire-resistant, all thanks to the natural chemical makeup of the grass, which contains traces of halogen and colloid.
In spite of all the periods of turbulence and socio-economic changes, Rongcheng is still home to 95,000 seaweed bungalows, the oldest of which has stood for 300 years.
Just 40 years ago, according to the local folklore expert Yu Yingyu, seaweed bungalows were common all along the eastern coastline of China, but they are rarely found beyond Rongcheng now.
Apart from modern aesthetics, most people find that building a seaweed thatched house is not an efficient process, by modern standards.
It usually takes a team of people more than a dozen days to build a seaweed thatch roof using 5,000 kilograms of eel grass. Skilled artisans pile up the dried seaweed layer upon layer on slanted sleepers on the roof, which can be as high as four meters. A layer of wheat straw buttressed between the seaweed make the whole structure sturdier.
To secure the roof against strong winds, villagers would usually cover the finished roof with a fishnet secured by cornerstones.
It is a dying craft, and many of the old craftsmen can no longer climb up the roofs.
Liu Yuqi, 52, is one of the "three to five artisans in a village who're still young enough to work".
Young people are too attracted by the city life to carry on the old art, he says, and the learning process itself is hard. It usually requires at least five years of training before an apprentice can start out on his own.
But Liu believes the job is still attractive. It's well paid, and craftsmen get at least 100 yuan ($16) a day and free meals. There is still a market, although it strays a little from the traditional targets.
In addition to all the repair jobs on existing roofs, Liu also finds plenty of work with the hotels and resorts who try to replicate the traditional architecture of the region.
There is also an attempt to bring the remaining craftsmen together to promote the art as a heritage craft and to bring it to places like Beijing and Shanghai.
The city government has also invested in efforts to promote the seaweed bungalows as a cultural heritage.
But yet another specter looms and threatens. Yu Shoushui says eel grasses are no longer commonly available, threatened by artificial and natural environmental degradation.
As new supplies dry up, villagers have to buy recycled grasses from demolished houses for their repair jobs. "But the good thing is, my house is strong enough to withstand another decade," says Yu, who has only repaired his roof twice and is very proud that his traditional home is so durable.
Contact the writer at hanbingbin@chinadaily.com.cn.
Ju Chuanjiang contributed to the story.
By Han Bingbin